Predictive Maintenance: How AI is Transforming Manufacturing
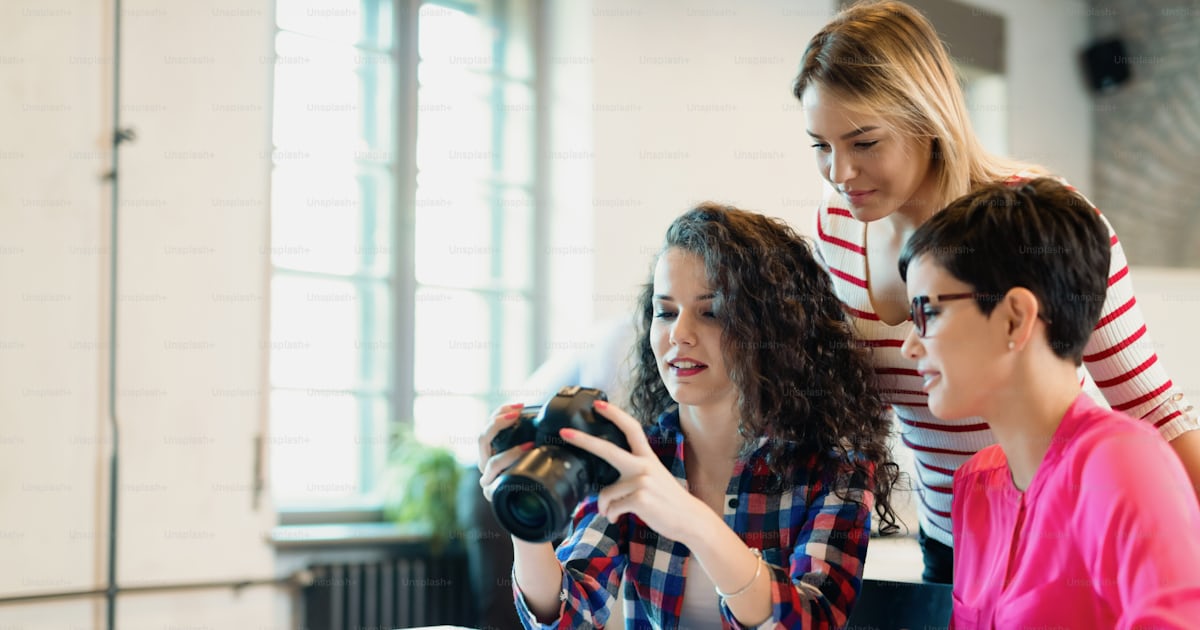
Venkat Sethuraman
September 25, 2023
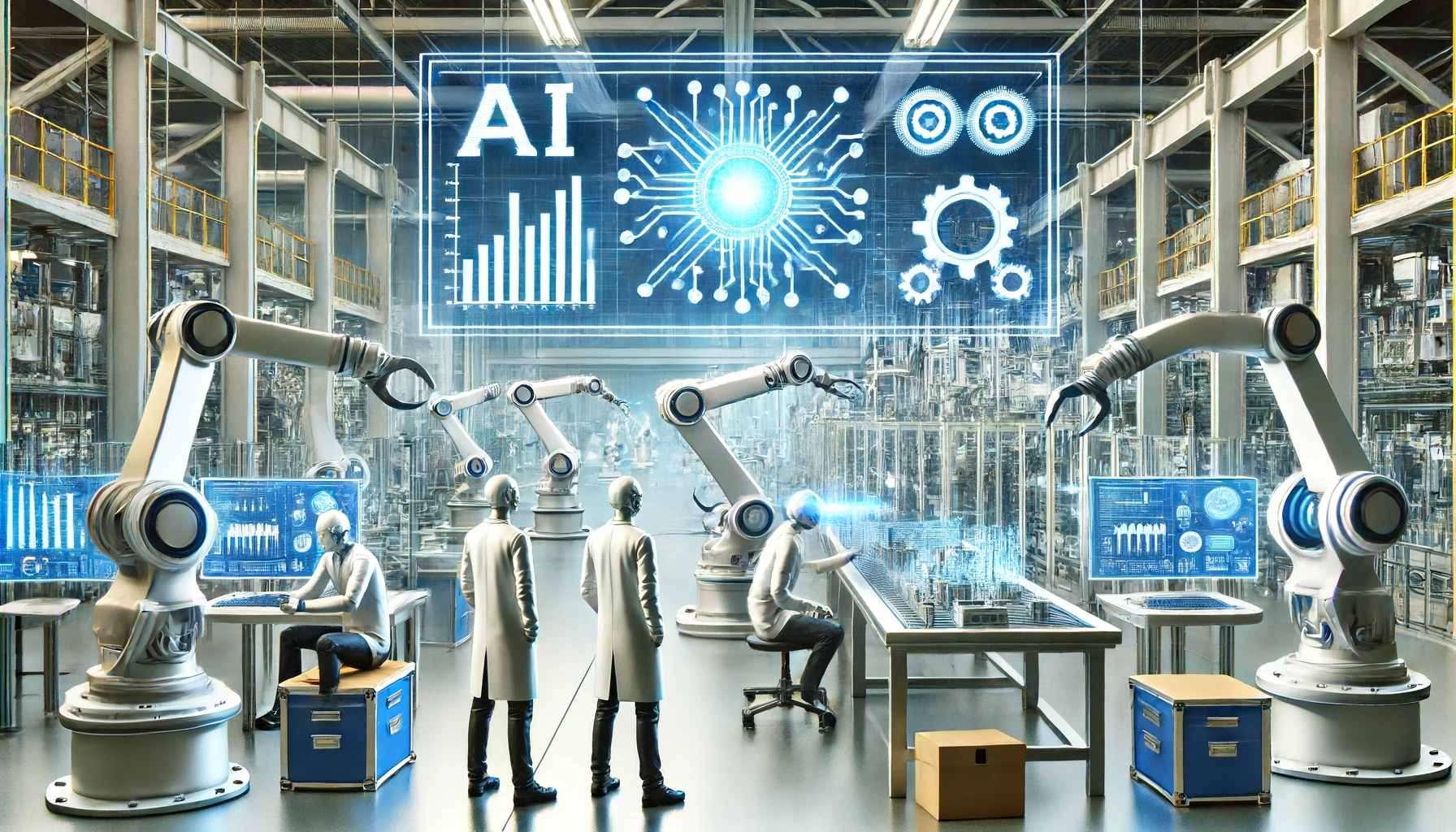
In the manufacturing industry, unplanned downtime is one of the most significant challenges, costing industrial manufacturers an estimated $50 billion annually. Traditional maintenance approaches—either reactive (fixing equipment after it breaks) or preventive (performing maintenance on a fixed schedule)—are increasingly inadequate in today's competitive environment. Predictive maintenance, powered by artificial intelligence, offers a more effective alternative.
The Evolution of Maintenance Strategies
To understand the value of AI-driven predictive maintenance, it's helpful to consider the evolution of maintenance strategies:
Reactive Maintenance
The "run until failure" approach, where equipment is only serviced after it breaks down. While this minimizes planned maintenance costs, it leads to unpredictable downtime, higher repair costs, and potential safety issues.
Preventive Maintenance
Maintenance performed on a fixed schedule based on time or usage metrics. While more effective than reactive maintenance, this approach often results in unnecessary maintenance activities and doesn't account for the actual condition of the equipment.
Condition-Based Maintenance
Maintenance triggered by observed changes in equipment parameters. This approach is more efficient than preventive maintenance but still primarily reactive rather than predictive.
Predictive Maintenance
Using data analysis and machine learning to predict when equipment is likely to fail, allowing maintenance to be scheduled just before problems occur. This approach minimizes both unnecessary maintenance and unexpected failures.
How AI Enables Predictive Maintenance
Artificial intelligence, particularly machine learning, is the key technology enabling effective predictive maintenance. Here's how it works:
Data Collection
Sensors installed on manufacturing equipment continuously collect data on various parameters such as temperature, vibration, pressure, sound, and electrical current. This Internet of Things (IoT) infrastructure generates vast amounts of data that would be impossible for humans to analyze manually.
Data Processing and Analysis
AI algorithms process this sensor data, along with historical maintenance records, to identify patterns and anomalies that may indicate potential failures. These algorithms can detect subtle changes in equipment behavior that might be imperceptible to human operators.
Failure Prediction
Machine learning models, trained on historical failure data, can predict when equipment is likely to fail. These predictions become more accurate over time as the models learn from new data and outcomes.
Maintenance Recommendations
Based on these predictions, the system generates maintenance recommendations, specifying what components need attention, when maintenance should be performed, and what actions should be taken.
Types of AI Models Used in Predictive Maintenance
Supervised Learning
When historical failure data is available, supervised learning models can be trained to recognize patterns that precede failures. Common algorithms include random forests, support vector machines, and neural networks.
Unsupervised Learning
When labeled failure data is limited, unsupervised learning techniques can identify anomalies in equipment behavior that may indicate potential issues. Clustering algorithms and autoencoders are commonly used for this purpose.
Time Series Analysis
Since equipment sensor data is typically collected over time, time series analysis techniques are particularly valuable. Recurrent neural networks (RNNs) and long short-term memory (LSTM) networks are effective for capturing temporal dependencies in the data.
Digital Twins
Advanced predictive maintenance systems may create "digital twins"—virtual replicas of physical equipment that simulate behavior under various conditions. These models can predict how equipment will respond to different operating parameters and maintenance interventions.
Benefits of AI-Driven Predictive Maintenance
Our implementations of predictive maintenance solutions have delivered significant benefits to manufacturing clients:
Reduced Downtime
By predicting failures before they occur, companies can schedule maintenance during planned downtime, reducing unplanned outages by up to 45%.
Extended Equipment Life
Addressing issues before they cause major damage extends the useful life of equipment by an average of 30%.
Lower Maintenance Costs
Predictive maintenance reduces costs by 15-30% compared to preventive maintenance by eliminating unnecessary maintenance activities and preventing costly emergency repairs.
Improved Safety
Preventing equipment failures reduces the risk of accidents and improves workplace safety.
Optimized Inventory Management
With better prediction of part failures, companies can optimize spare parts inventory, reducing carrying costs while ensuring parts are available when needed.
Enhanced Production Quality
Equipment operating at optimal conditions produces higher quality output with fewer defects.
Implementation Challenges and Solutions
While the benefits of AI-driven predictive maintenance are compelling, implementation comes with challenges:
Data Quality and Quantity
Effective predictive maintenance requires sufficient high-quality data. For companies with limited historical data, we recommend starting with a hybrid approach that combines available data with expert knowledge, gradually building more sophisticated models as more data becomes available.
Integration with Existing Systems
Predictive maintenance solutions must integrate with existing enterprise systems such as ERP, MES, and CMMS. Our solutions are designed with open APIs and flexible integration options to address this challenge.
Organizational Change
Implementing predictive maintenance requires changes to established maintenance processes and workflows. We provide change management support and training to help organizations successfully adopt new approaches.
ROI Justification
The initial investment in sensors, infrastructure, and analytics can be substantial. We help clients develop phased implementation plans that deliver quick wins to demonstrate value before scaling to enterprise-wide deployment.
Case Study: Predictive Maintenance Success
One of our manufacturing clients implemented our AI-driven predictive maintenance solution across their production facilities with impressive results:
- 45% reduction in unplanned downtime
- 30% increase in equipment lifespan
- 22% decrease in maintenance costs
- 15% improvement in production efficiency
- ROI achieved within 9 months of implementation
The Future of Predictive Maintenance
As AI technology continues to evolve, we anticipate several exciting developments in predictive maintenance:
Edge Computing
Processing data closer to its source will enable real-time analysis and faster response to potential issues, even in environments with limited connectivity.
Augmented Reality
Maintenance technicians will use AR devices that overlay diagnostic information and repair instructions on physical equipment, improving efficiency and reducing errors.
Autonomous Maintenance
In some applications, AI systems will not only predict maintenance needs but also execute repairs using robotics and automation, further reducing downtime.
Cross-Asset Optimization
Future systems will optimize maintenance across entire production lines or facilities, considering the interdependencies between different pieces of equipment.
At Xylia.ai, we're at the forefront of these developments, continuously enhancing our predictive maintenance solutions to deliver even greater value to our manufacturing clients. By combining cutting-edge AI technology with deep domain expertise, we're helping manufacturers transform their maintenance operations from a cost center to a strategic advantage.